Ryan E. Day | Contributing Editor / Content-Marketing Coordinator | Quality Digest | 20. Januar 2020
Plasser American nutzt FARO® Laserprojektion und Laserscanner-Technologie zur Verbesserung der Effizienz und Erhöhung des Durchsatzes
Mit mehr als 300 Mitarbeitern in einer modernen, über 150.000 Quadratmeter großen Anlage stellt Plasser American Corporation (PAC) hochwertige schwere Eisenbahnbau- und Wartungsgeräte für Kunden in Nordamerika her. Um auf diesem internationalen Markt wettbewerbsfähig zu bleiben, sucht PAC ständig nach Möglichkeiten, seine Prozesse und Best Practices zu verbessern.
"Wir haben uns zum Ziel gesetzt, die Nacharbeit beim Schweißen im Montagebereich drastisch zu reduzieren, so dass alle Schweißarbeiten an den einzelnen Bauteilen unserer Rahmen in der Rahmenwerkstatt beim ersten Schweißen durchgeführt werden", erklärt Joe Stark, Vice President of Operations and Production. "Zu dieser Zeit haben wir jede Maschine, die wir gebaut haben, von Hand mit Maßband und Speckstein ausgelegt. Unsere Konsistenz von Maschine zu Maschine war einfach nicht so, wie sie sein sollte, was bedeutete, dass zu viele Nacharbeiten in den Hauptmontagebereichen durchgeführt werden mussten. Wir wussten, dass wir eine gewisse Standardisierung und Best Practices entwickeln mussten, um unsere Ziele zu erreichen."
Herausforderung
Das Plasser-Team prüfte die Möglichkeit, dass seine Konstruktionsabteilung Modelle erstellt, in denen jede Lasche, Halterung, Platte usw. detailliert dargestellt wird. Die Idee wurde aufgrund des enormen Zeitaufwands verworfen, der erforderlich wäre, um die Modelle zu 100 % genau zu halten.
Aufgrund des Produktionsmixes war die Verwendung herkömmlicher Vorrichtungen keine praktikable Option.
"Wir sind ein Low-Run-High-Mix-Geschäft mit mehr als einem Dutzend Modellen, von denen jedes mehrere Iterationen sowie Kundenwünsche nach kundenspezifischen Anpassungen aufweist", sagt Anthony Dozier, Mechanik-Konstrukteur und Mechanik-Verbindungsingenieur bei Plasser American. "Es wäre sehr schwierig, Vorrichtungen an einige dieser Orte zu bringen, und bei einigen unserer Rahmen gibt es 400 bis 500 kleine Komponenten, die je nach Rahmenmodell und Iteration ausgelegt werden müssen. Es würde eine unangemessene Menge an Vorrichtungen benötigen, um diese Teile jedes Mal zu lokalisieren."
Entwickeln von Best Practices
Plassers erste Entwicklung von Best Practices für die Qualitätskontrolle bestand in der Verwendung von mobilen Geräten in der Werkstatt, um die Positionen von Unterbaugruppen anzuzeigen.
"Sobald wir ein Teil auf einem Rahmen ausgelegt haben, haben wir ein Foto davon gemacht", sagt Stark. "Das konnte dann mit einem Referenzpunkt angezeigt werden. Wir hätten also die Abmessungen und würden die Teilenummer auf das Teil schreiben. Aber es stellte sich heraus, dass es ein sehr manueller Prozess war; die Schweißer und Monteure, die das Layout machten, mussten das mobile Gerät immer noch bei sich haben, und wir waren immer noch darauf angewiesen, dass jemand ein Maßband benutzte und ein Teil festhielt, während er es heftete. Auch wenn es eine Verbesserung war, waren wir immer noch nicht da, wo wir sein müssten."
Auch die Dokumentenkontrolle war recht zeitaufwändig. Das PAC-Team arbeitete weiter an der Verbesserung seiner Prozesse.
Lösung
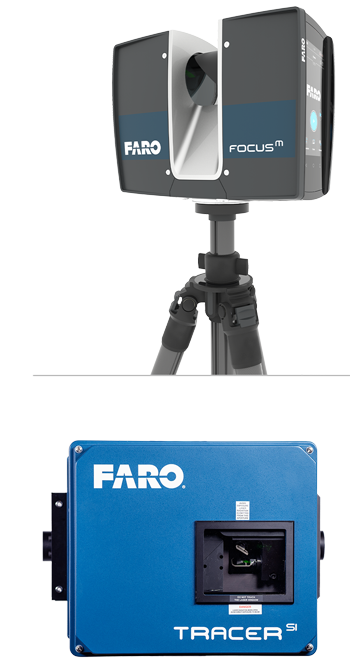
"Wir haben weiter nach Möglichkeiten gesucht, wie wir unsere Effizienz steigern und unsere Qualitätskontrolle verbessern können. Wir beschlossen, dass die Laserprojektionstechnologie eine gute Lösung sein könnte", sagt Stark. "Wenn wir auf den Rahmen projizieren könnten, wo all diese Einzelteile hingehören, könnte das unsere Konsistenz von einer Maschine zur nächsten verbessern und uns auch dabei helfen, mehrere Phasen des Baus zu standardisieren."
Das Plasser-Team investierte in den FARO FocusM 70 Laserscanner und einen FARO TracerSI Laserprojektor.
"Wir beschlossen, dass wir für den ersten Maschinenrahmen eines Typs, den wir bauen, weiterhin unser manuelles Layout-Verfahren verwenden würden", erklärt Stark. "Dann können wir das als komplettes Modell mit dem FocusM scannen und unsere CAD-Dateien mit den Scandaten aktualisieren. Die CAD-Dateien werden dann zur Erstellung von Projektordateien verwendet, damit der TracerSI die Positionen der Komponenten auf den nächsten Rahmen des Modells projizieren kann, das wir bauen. Wir machen gerade einen kompletten Scan von allem, was wir bauen, damit wir mit dem Aufbau einer Bibliothek beginnen können."
Ergebnisse
„Es hilft enorm, den Standort von Komponenten zu erfassen, die für die technische Seite des Designs nicht unbedingt kritisch sind“, erklärt Dozier. „Es gibt jedoch viele Kabelwege, Schutz- und Stützplatten, die zwar für das technische Design nicht kritisch sind, aber für den tatsächlichen Aufbau der Maschine von enormer Bedeutung sind. Sobald wir diese Informationen gescannt und erfasst und die Konstruktionsdokumentation aktualisiert haben, um die Komponentennamen und -positionen einzuschließen, können wir diese Elemente aktualisieren und einfach auf die Maschinenrahmen projizieren, während wir sie erstellen. “
Die Vorteile der Laserprojektion waren erheblich und wurden zur neuen Best Practice.
„Bevor wir dieses Setup hatten, konnten wir leicht ein halbes Dutzend oder mehr Leute haben, die die Layoutarbeit erledigten“, gibt Stark zu. „Jetzt haben wir eine Person, die Schweißkomponenten gemäß der Projektion auslegt und anheftet, und eine andere Person, die dahinter kommt und die Endschweißung durchführt. Wir haben die Zeit für den Layoutprozess um etwa fünfzig Prozent verkürzt. “
Mit dem FARO-Setup konnte Plasser nicht nur erhebliche Produktivitätssteigerungen verzeichnen, sondern auch Prozessverbesserungen erzielen.
„Durch den Detaillierungsgrad, den der Scanner bietet, können wir alle Schweißplatten vorab herstellen“, sagt Stark. „Da wir 100% der Komponenteninformationen erfasst haben, ist unsere Stückliste jetzt 100% genau. Wir können alle verschiedenen Komponenten und Schweißplatten vorab herstellen, damit sie am Rahmen befestigt werden können. “
Sammeln und Dokumentieren von Komponenteninformationen auf einer gesamten Maschine kann von Hand vier Wochen dauern. Mit unserer FARO-Ausrüstung dauert es jetzt zwei Tage, um dieselben Informationen zu erfassen.
Anthony Dozier
Maschinenbauingenieur und Verbindungsingenieur, Plasser American
Das Plasser-Team stellte fest, dass der Tracer SI sowohl als Inspektionswerkzeug als auch als Montagewerkzeug nützlich sein kann. Der unerwartete Vorteil hilft Plasser, Nacharbeiten zu minimieren. Sie verwenden den Tracer S I, um die Inspektion in zwei wichtigen Schritten des Herstellungsprozesses auf zwei Arten durchzuführen: Erstens bieten die Projektorlinien eine Methode zur visuellen Überprüfung der Baugruppe, wenn der Tracer SI auf die Bestandsbaugruppe projiziert. Zweitens ist der Tracer SI mehr als nur ein Laserprojektor - er ist der einzige Imaging-Laserprojektor auf dem Markt und bietet IPV (In-Process Verification). Sobald die Komponenten mit dem Rahmen verschweißt sind, scannt der Tracer SI die Oberfläche mit hoher Auflösung und erkennt Fehler in Echtzeit. Es ist in der Lage, falsch platzierte Teile, fehlende Teile und Fremdkörperreste zu erkennen.
Darüber hinaus ermöglichen die Bildgebungsfunktionen des Tracer SI Plasser eine ziellose, merkmalsbasierte Ausrichtung. Bei anderen Laserprojektoren müssen Retroreflektoren verwendet werden, damit der Projektor richtig auf der Arbeitsfläche ausgerichtet werden kann. Die Verwendung von Retroreflektoren erfordert zusätzliche Schritte. Mit dem Tracer SI können die tatsächlichen Merkmale wie Löcher oder Kanten der Arbeitsfläche anstelle (oder zusätzlich zu) Retroreflektoren verwendet werden, um Zeit und Mühe zu sparen. „Plasser stellt massive Maschinen her und an vielen Stellen des Rahmens können wir keinen definierten Punkt verwenden, um ein Retro-Ziel zu platzieren. In vielen Fällen sind Lochmuster oder kleinere Strukturrahmenelemente unsere besten Optionen für die Ausrichtung, und hier hat sich die ziellose Ausrichtung als vorteilhaft erwiesen “, fügte Dozier hinzu.
"Wir haben einen deutlichen Rückgang der Nacharbeit festgestellt", sagt Stark. "Es ist leicht, einen Fehler zu machen, wenn man Hunderte von Teilen auf einem einzigen Rahmen platziert. Wenn man den Fehler erst in der Montagephase des Rahmens bemerkt, kann sich das Ausmaß der Nacharbeit um ein Vielfaches erhöhen. Es kann sein, dass Sie z. B. die Verdrahtung rückgängig machen und neu machen müssen und dann den Bereich nach der Nacharbeit neu lackieren müssen."
Als sie gebeten wurden, die kombinierte Lösung aus Focus Laser Scanner und TracerSI von FARO nach verschiedenen Kriterien zu bewerten, gaben Stark und Dozier die folgenden Bewertungen ab:
Kriterien: | Bewertung: |
Genauigkeit und Wiederholbarkeit | Spielveränderer |
Geschwindigkeit der Messung | Spielveränderer |
Benutzerfreundlichkeit | Spielveränderer |
Tragbarkeit | Spielveränderer |