Advance in Metalworking, Machining and Assembly
FARO solutions ensure accuracy and quality control.
With applications ranging from the largest aircraft carrier to myriads of precision component parts, the metalworking, machining and assembly industry is essential to the global economy. Accuracy is key for forming, joining and cutting metals. With a wide selection of portable precision measurement solutions from FARO, you can measure parts with great accuracy, right on the shop floor — arriving at answers sooner and gaining from the experience.
Reach perfection through precision in your metalworking operations
Quality Engineers
Reduce costs by managing enhanced process efficiencies.
Tool Builders
Create and align tooling during assembly or sub-assembly with new approaches and technologies.
Production Engineers
Increase the number and/or frequency of alignments, while eliminating human error.
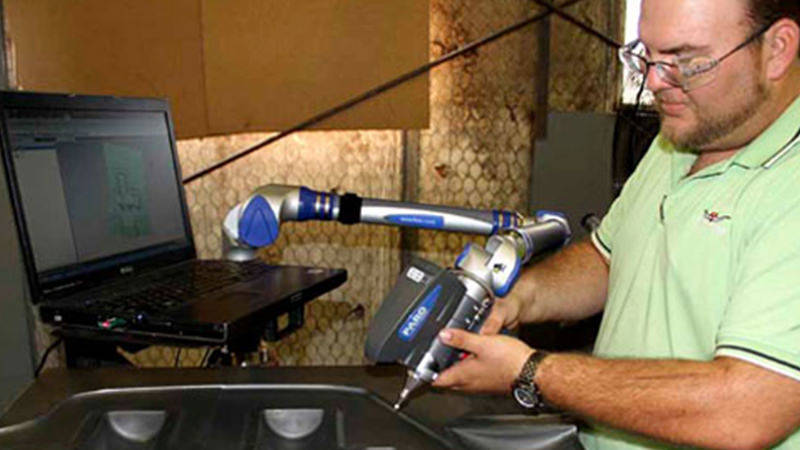
Case Study
Trinity Forge Sees Triple Benefit
The Houston-based closed-die forging plant uses FARO technology to provide job-shop and die-and-mold machining services with slashed inspection times.
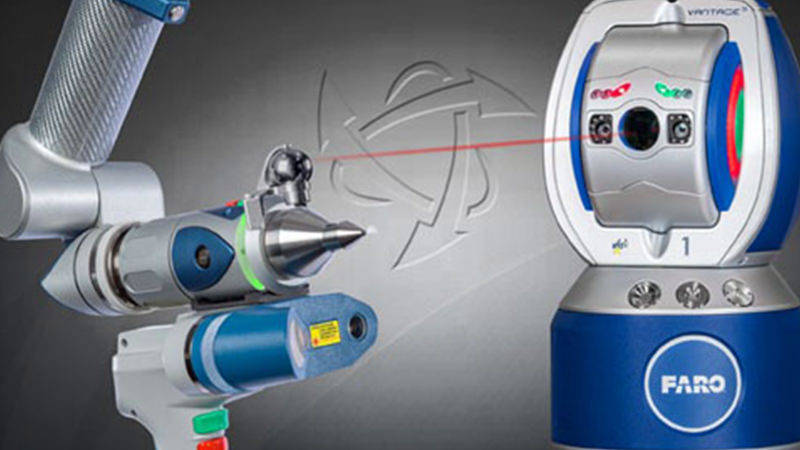
Case Study
Janicki Industries Cuts Machining Time
The 27-year-old aerospace tooling company employs a FARO Laser Tracker and ScanArm to achieve a 35% reduction in required machining.
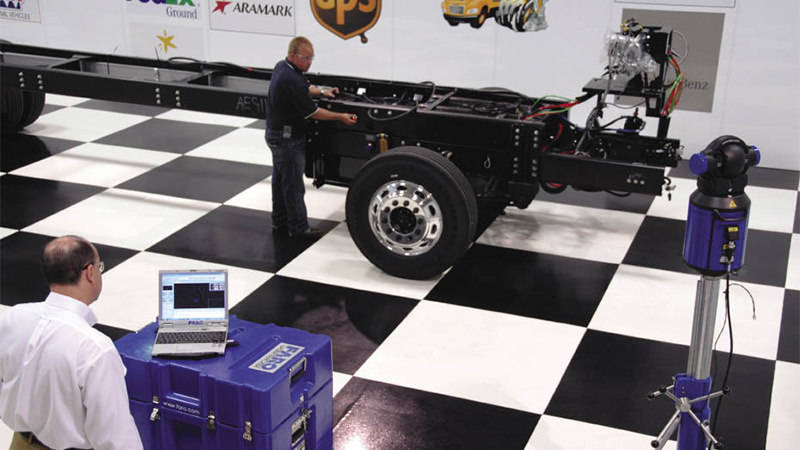
Case Study
Freightliner Custom Chassis Reduces Rework
The company’s quality action team cut inspection times from 4 hours to 15 minutes with the FARO Vantage Laser Tracker.
Metalworking Insights
When you work with FARO, you benefit from our years of experience helping a wide range of metalworking machine manufacturers hone their operations. We’ve collected all our insights in a library of resources for you.
Metalworking Product Spotlight
Quantum X FaroArms
Learn how the Quantum X FaroArm Series delivers up to a 15% accuracy improvement over existing Faro Arms.
FARO Vantage Laser Trackers
Proving the way forward for fast and accurate measurements for assembly, alignment and reverse-engineering needs.
FARO Tracer Laser Projectors
Project an accurate laser outline onto a 3D surface or object; ideal for composite layup applications.
FARO® Leap ST® Handheld 3D Scanner
The FARO® Leap ST™ is an exciting next step in metrology-grade handheld laser scanning. Learn how its five operating modes boost productivity and business value.
Makes prototype inspection a lot easier.
Mark Kalp
Wheeler Bros Inc.
Using the FaroArm, we are now able to check and rework until our parts are in perfect tolerance with the CAD models. This accuracy has gained us customers, and now we are able to have work sent to us, just to be scanned, and returned. This arm has created multiple new jobs for us!
Jordan Parker
Diversified Pattern & Engineering Co Inc.
Accuracy and repeatability [have] been greatly improved on the floor, and it’s so easy to take around the warehouse.
Jason Chen
O’Neal Steel Inc.