Quality Control and Inspection
Meeting quality requirements with 3D measurement solutions
Improve your quality control and inspection processes, whether you need to catch errors earlier in the manufacturing process or reduce your overall rework and scrap.
Solve Your Quality Problems with FARO
In order to stay competitive, you need to meet ever-stricter quality standards — but you have to do it as cost-effectively as possible. You can’t invest in a quality control or inspection solution only to find out that it doesn’t perform as you expected, or that it requires significant changes to your team’s workflow, skills or software. At FARO, we understand. That’s why we’ve developed our 3D measurement technologies and quality control inspection software to integrate with your existing systems so you can take your operations to the next level of excellence with complete support every step of the way.
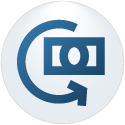
Provable ROI
When you choose FARO, your quality improvements will help you quickly recoup the cost of the solution and drive increased profitability.
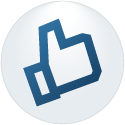
Ease of Use
Even your non-technical team members will be able to use FARO equipment correctly, ensuring inspection accuracy and speed. Data and reporting outputs are accessible and easy to understand.
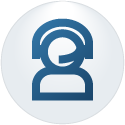
Reliable Post-sale Support
Rest assured that FARO provides immediate support to minimize downtime, as well as ongoing training for your expanding team.
Quality Control and Inspection Solutions
FARO 3D measurement technologies help manufacturers improve their quality control and inspection processes across a wide range of operations.
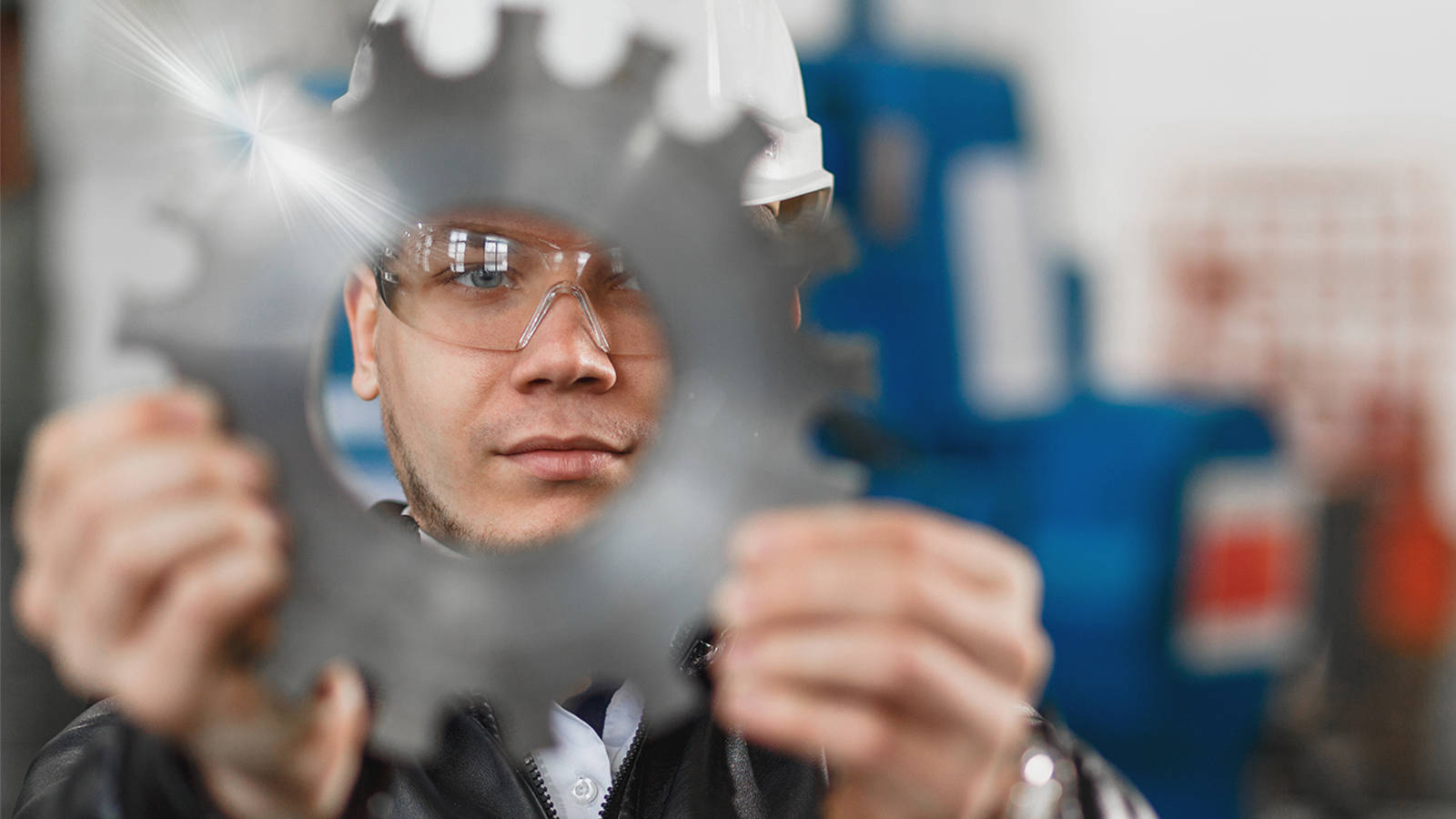
Machined Parts Inspection
Verify precision and accuracy of every machined part.
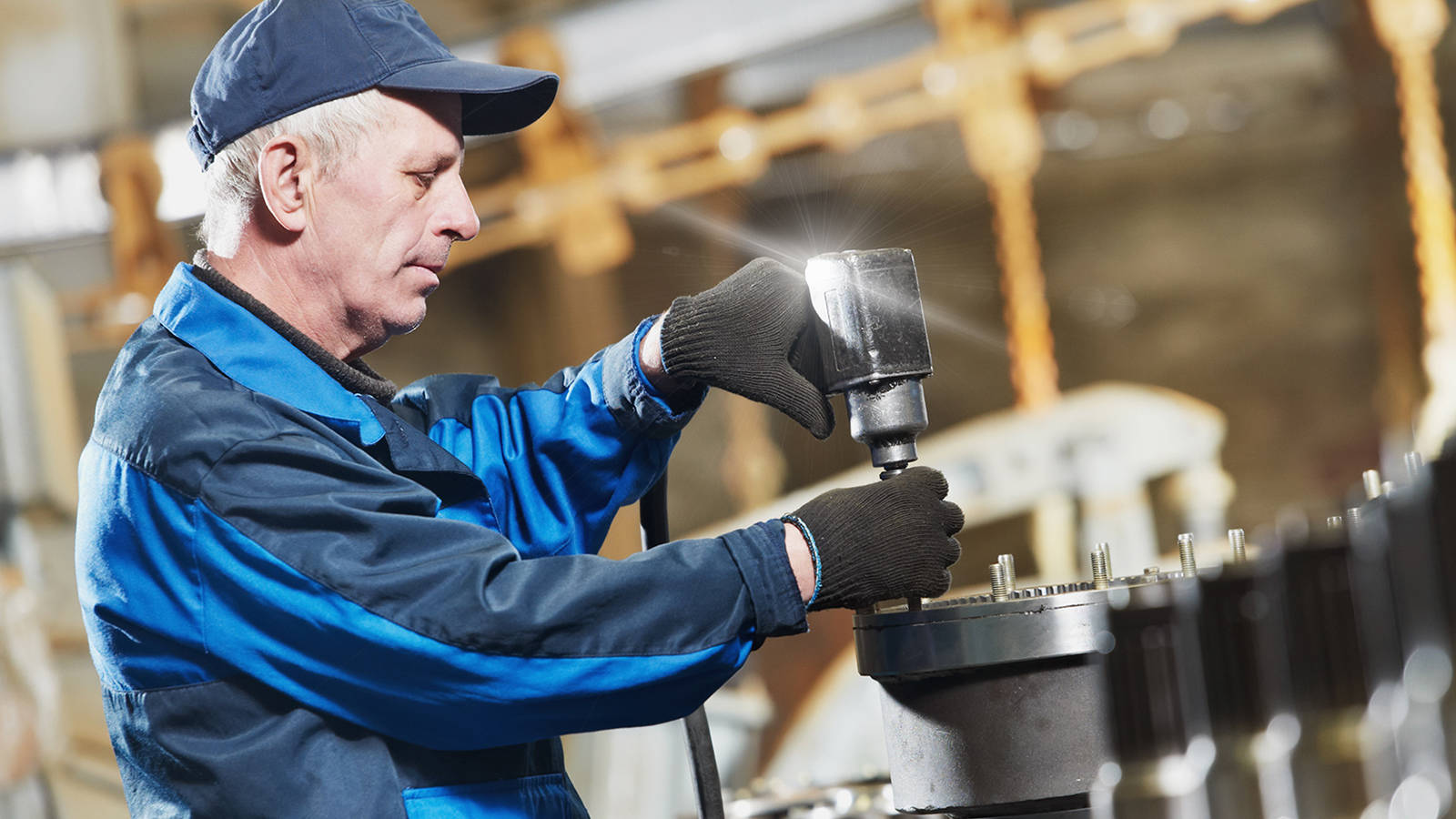
Parts Assembly Management
Take the complexity out of your most comprehensive assemblies.
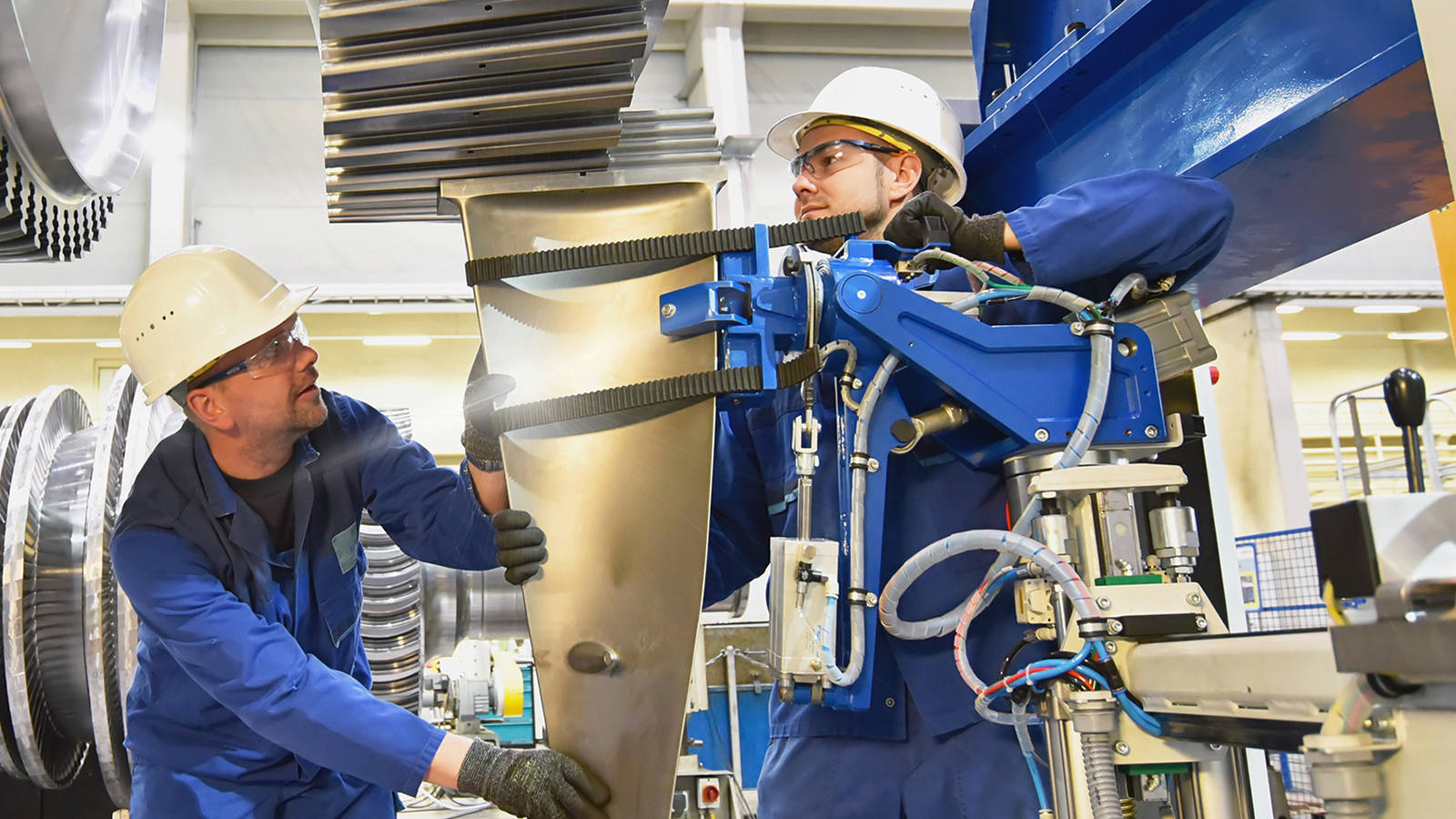
Large-scale Parts Assembly Management
Measure large parts with ease right on the assembly floor.
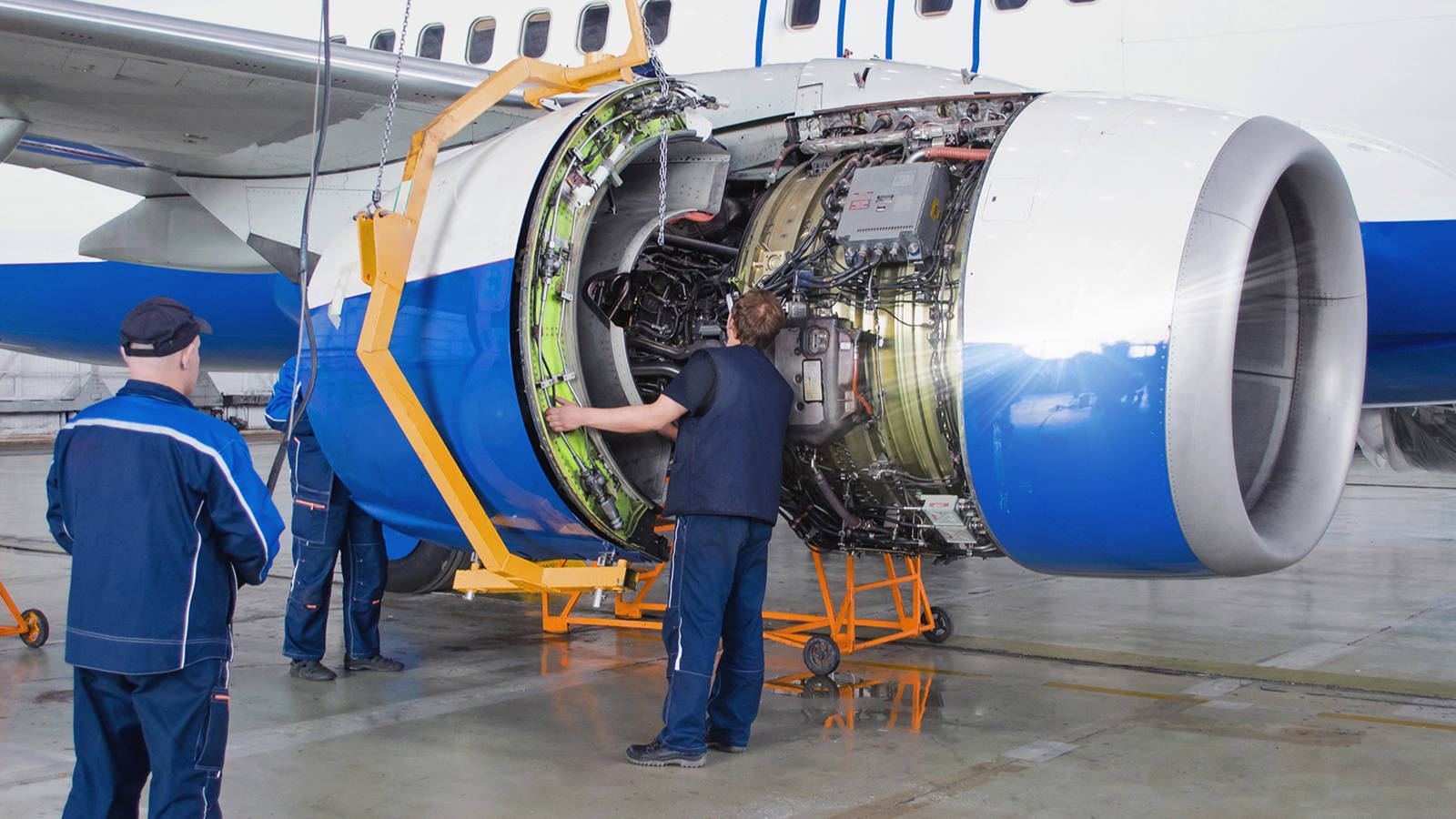
Tool Building Measurement
Ensure the accuracy of your tools and related components.
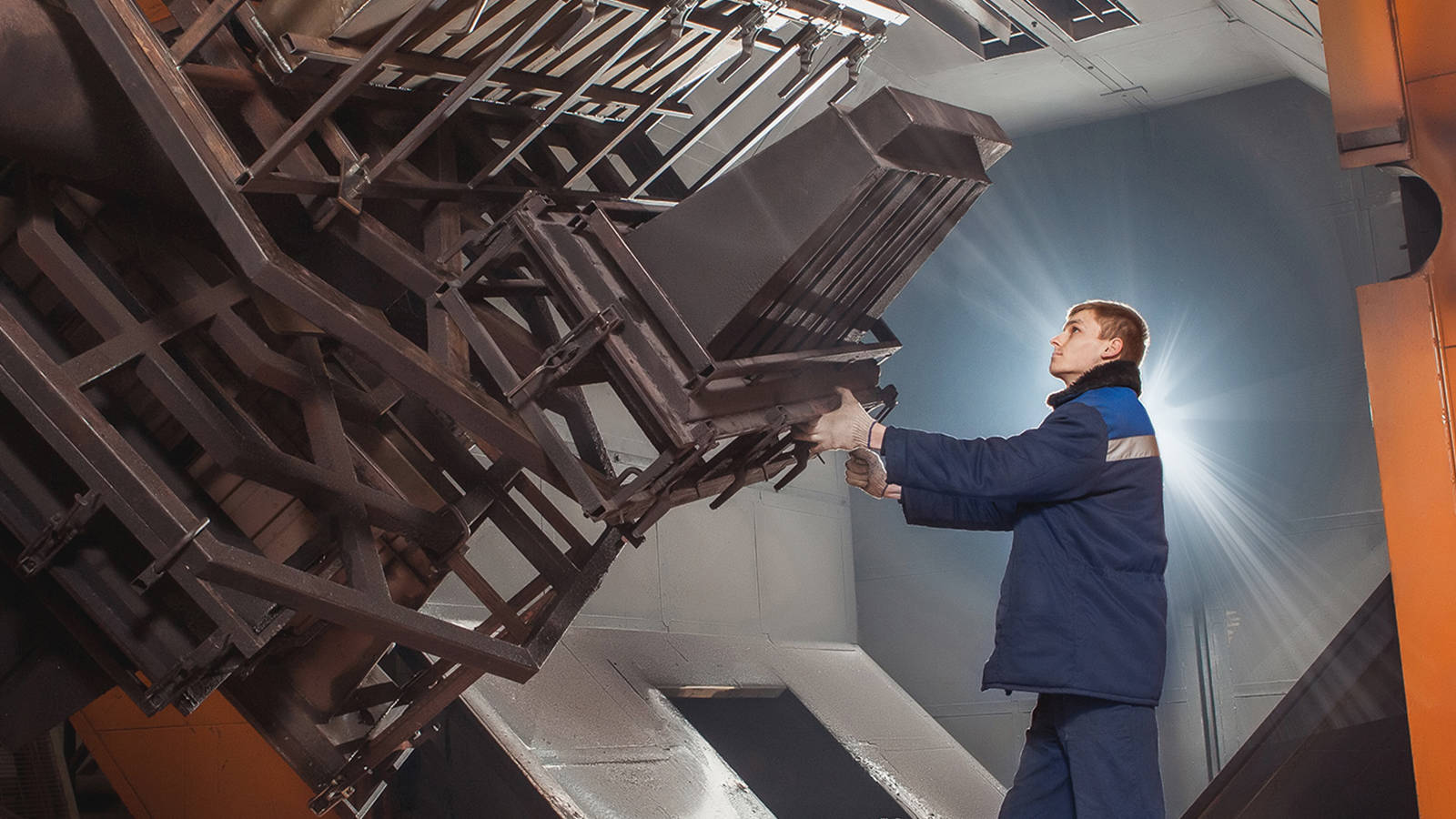
Injection Molding Inspection
Inspect or reverse-engineer molds and parts with the highest precision.
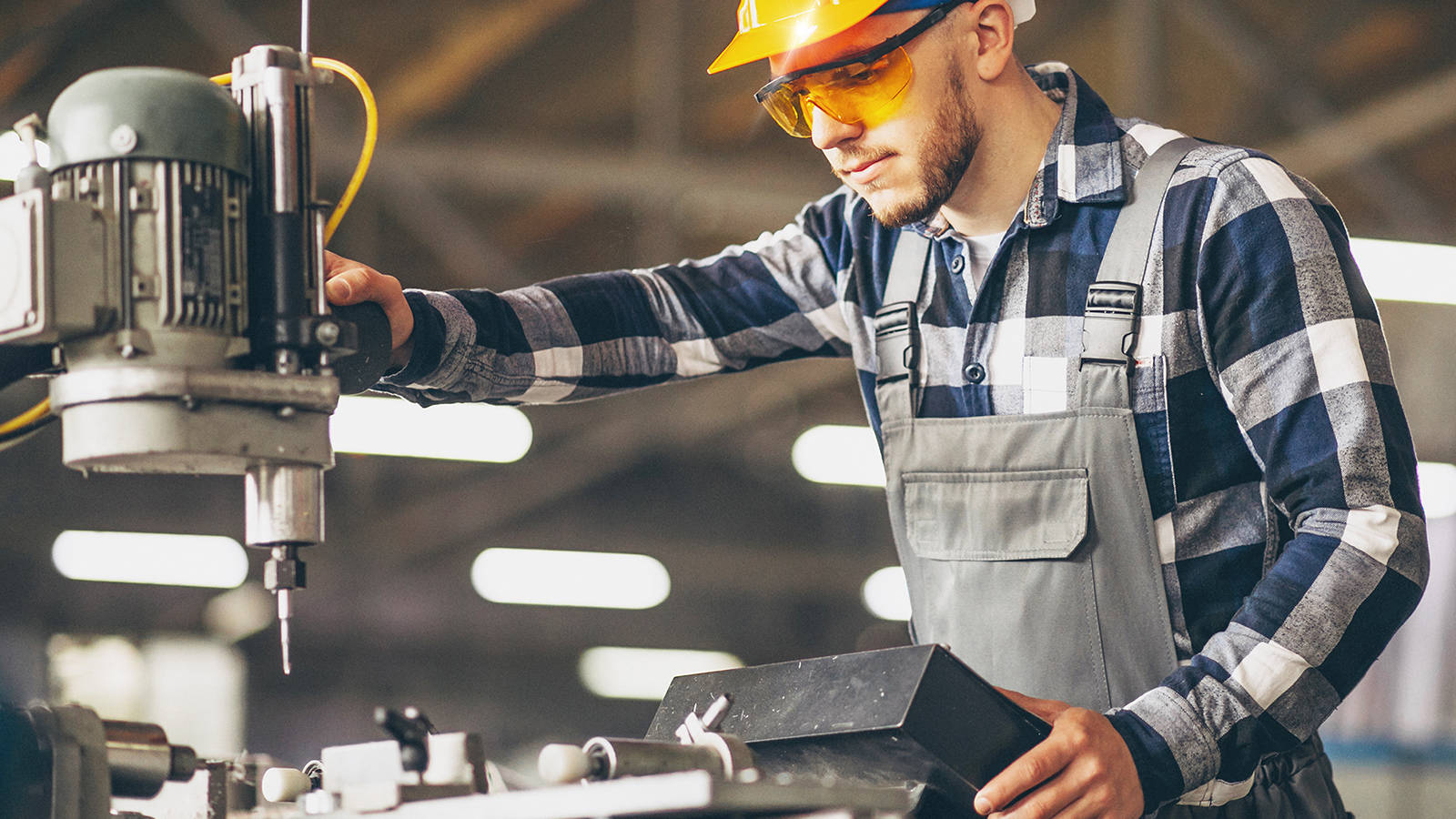
Forging
Forge ahead with 3D measurement tools to evaluate complex forged part geometry.
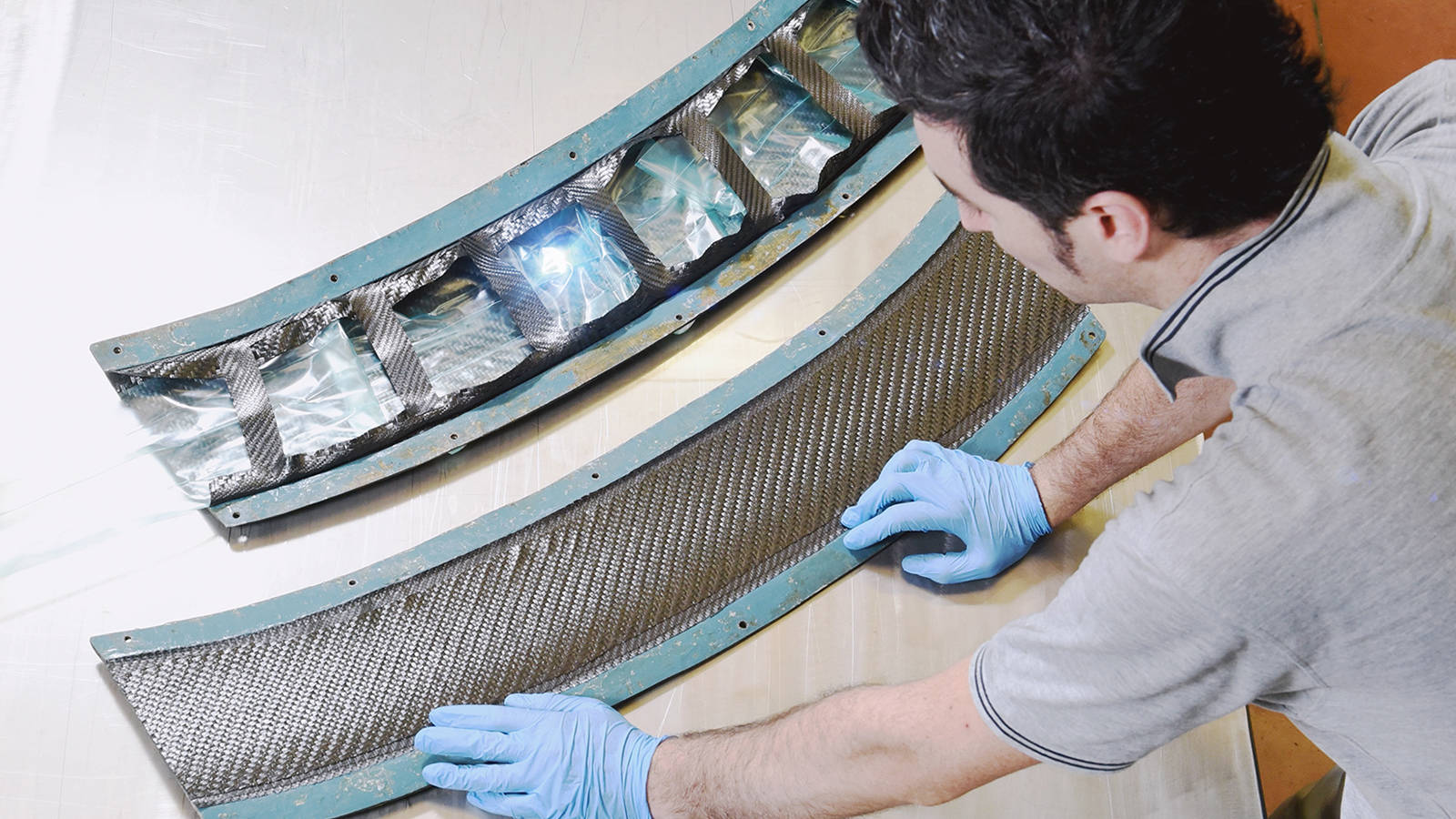
Composite Manufacturing and Inspection
Build with strength, flexibility, accuracy and safety.
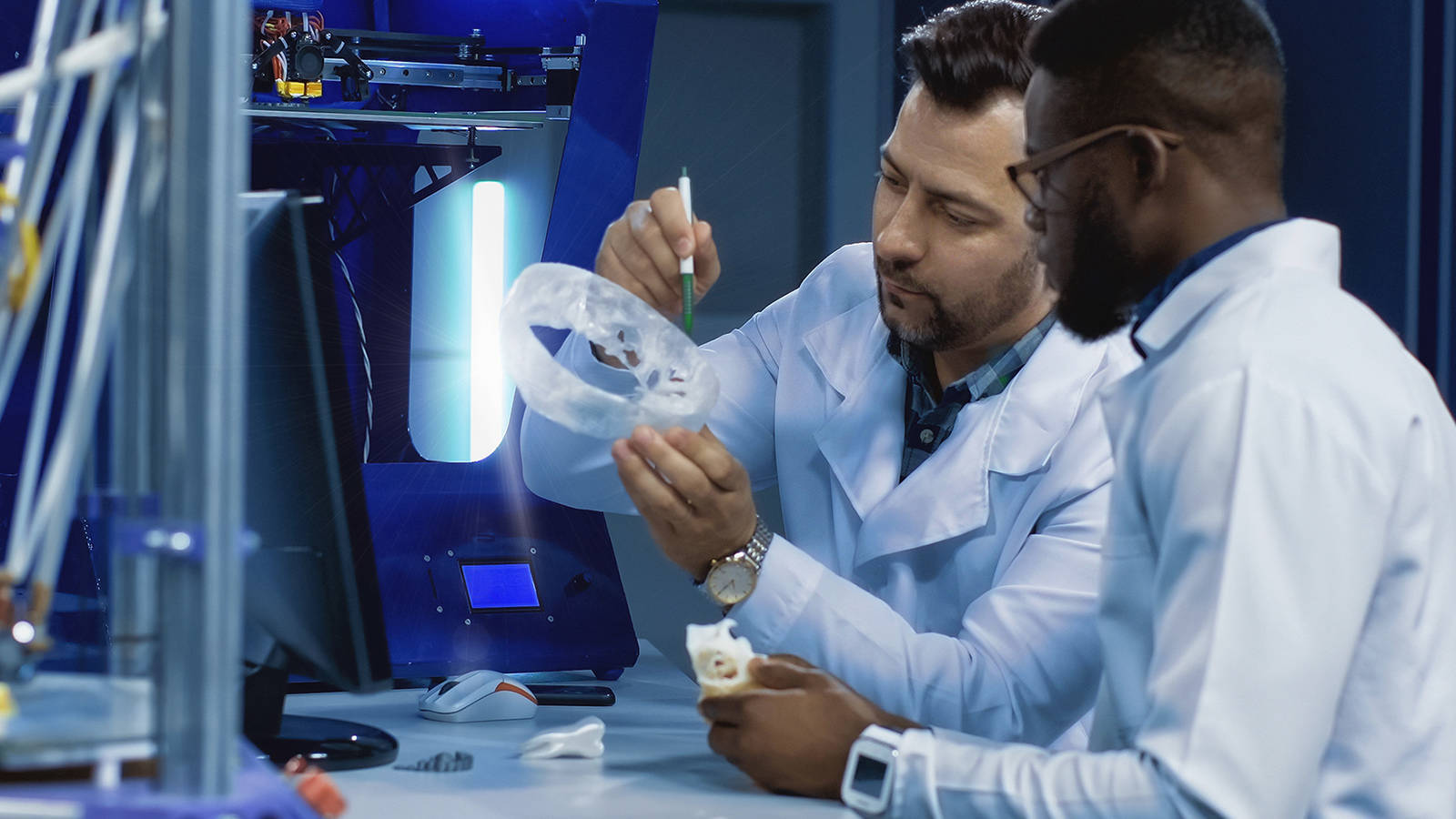
Additive Manufacturing
Ensure precision of parts built through additive manufacturing.
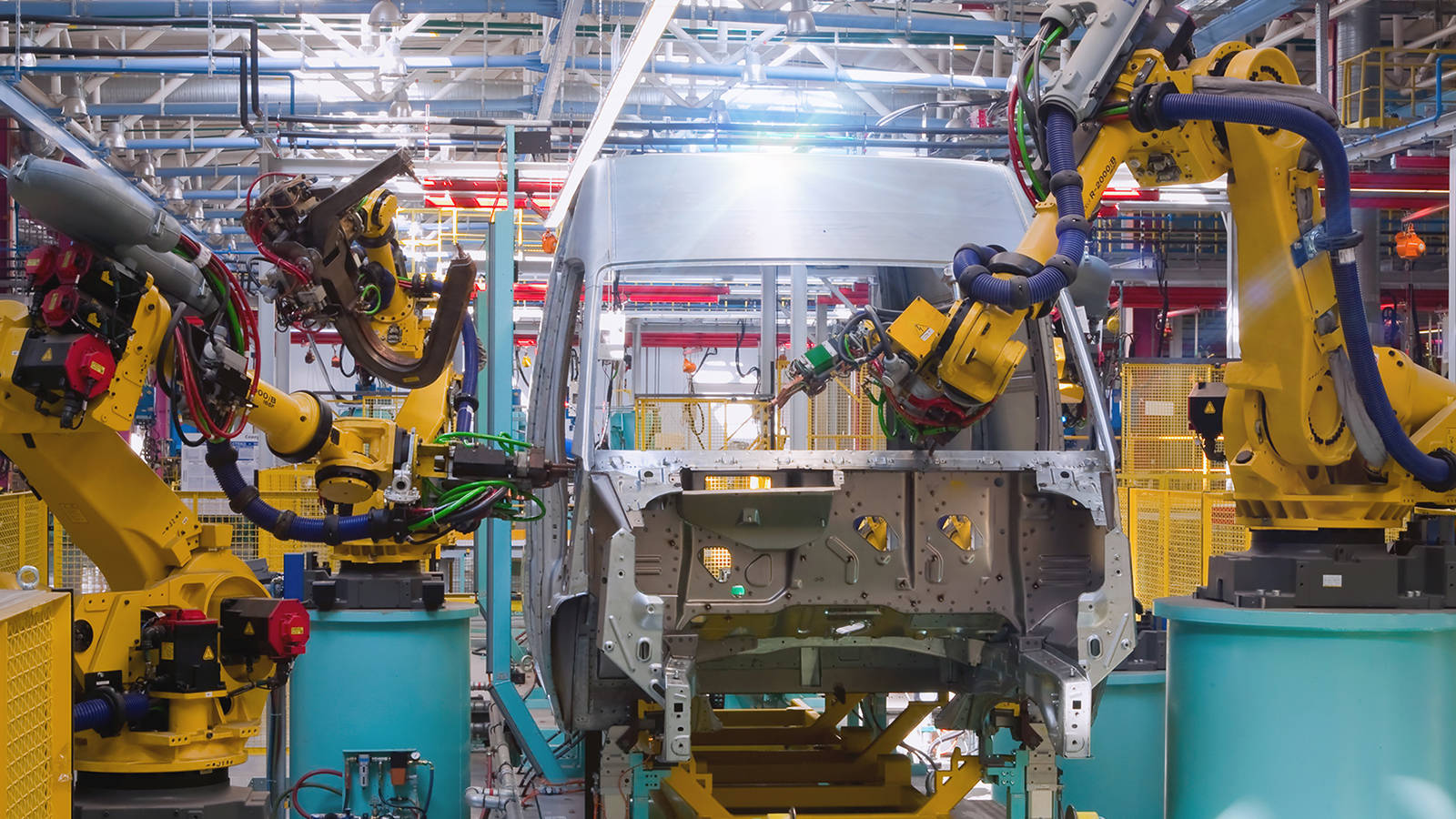
Industrial Automation Quality Control
Automate industrial processes and eliminate the guesswork in quality control.
I have found that their learning curve is relatively smooth and the software used with it makes for a straightforward approach for digital inspection and reverse engineering.
Zachary Herbert
Standard Forged Products
Excellent tool for part inspection and validation layout.
Jeffrey Harne
Ford Motor Company
Our FARO tool has been extremely useful in our manufacturing operations for checking critical dimensions and also to evaluate work pieces for customer requests.
Josh Ford
LMC Workholding
Case Studies Featuring FARO Quality Control Solutions
CASE STUDY
Airbus Reduces Inspection Cycle Time by 80%
The aircraft manufacturer uses a FARO solution to ensure accurate fuselage assembly.
CASE STUDY
Boeing Supplier of the Year Wins Jobs
Woodland Trade Co. lands tight-tolerance aerospace contracts, thanks to FARO.
CASE STUDY
Brodie International Saves Time and Cuts Scrap
The petroleum and industrial equipment provider improves the inspection process with FARO.
CASE STUDY
Manufacturer Builds Large Tooling with Tight Tolerances
An aerospace manufacturing superstar relies on FARO for precision measurement.
Speak with a Quality Control Expert
For 40 years, FARO has partnered with manufacturers to improve their quality control and inspection processes. We want to do the same for you.
Quality Control Insights
Find more case studies, videos, articles and other resources related to precision measurement and quality control.